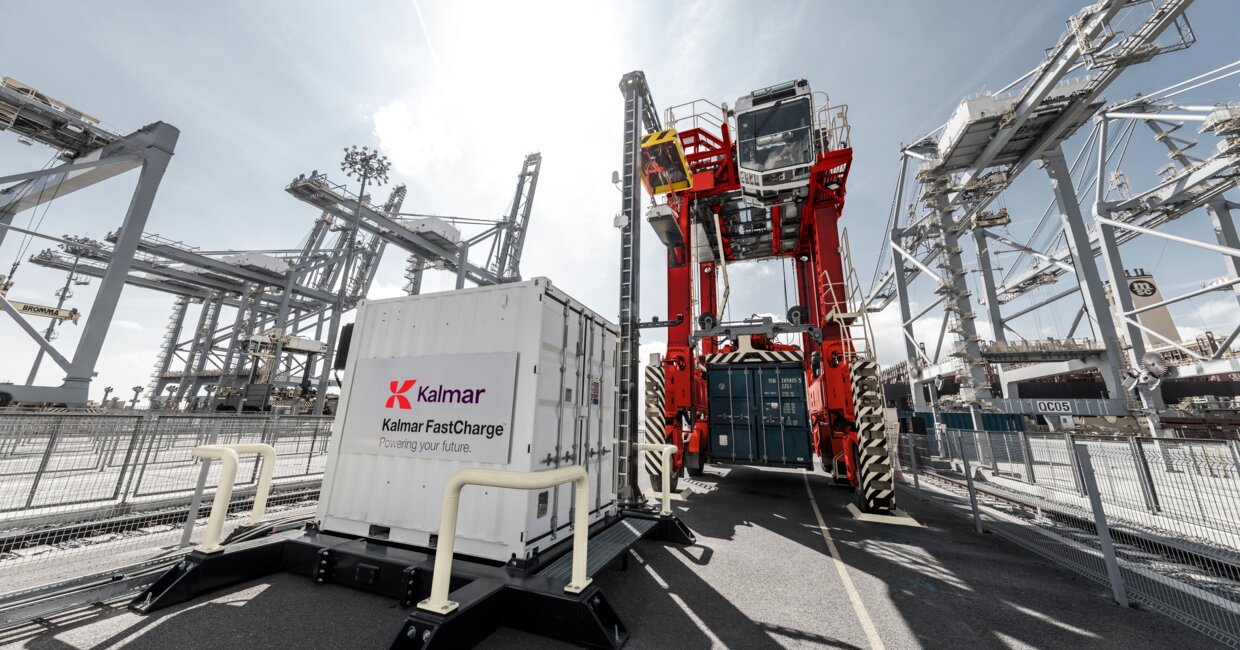
When and how to charge? Charging options for electric straddle carriers
Today's terminal operators face a common list of questions and concerns when planning their electrification journey. Will there be enough grid capacity and green power available to charge a fleet of electric machines? Will a shift to a new electric infrastructure require prohibitively large investments? How will the charging of battery-powered equipment affect everyday operations? And, finally, will more straddle carriers be required to reach the same terminal throughput? In this article, Kalmar's experts break down some of the key considerations and available options for electrifying straddle carrier terminals.
In an electric straddle carrier fleet, the technical choices of equipment types and charging system are directly linked to operational considerations. For example, the availability and capacity of grid power will affect the charge scheduling and optimisation for larger equipment fleets. Thus, any decision to electrify a straddle carrier fleet involves both operational and technical factors.
"On the operational side, there are few items that you should be thinking of, starting with the operating hours per day," says Mikko Nurmela, Senior Development Manager, Kalmar. "What kind of work time and break pattern you have in your operation will affect your charging needs, as will the type of duty cycle you are running, whether it is light, medium or heavy-duty operation."
The Kalmar Charge Family is an offering comprising battery technologies, charging solutions and software to support operators of both manual and automated terminals with their transition towards decarbonised operations. The family includes two different battery and charging technologies that can be deployed based on the individual operational needs of the terminal. The Kalmar electric straddle carrier with High Energy battery is capable of a minimum of four hours of continuous operation with a charging time of 45 to 50 minutes, while straddle carriers with High Power battery technology are capable of up to one hour of continuous operation with five to six minutes of charging using FastCharge technology.
The High Energy batteries are designed for an operational model in which the machines are charged during lunchtime or other breaks that occur naturally in the operation. By contrast, High Power battery technology (previously known as Kalmar FastCharge™ technology) is designed for opportunity charging during operations. "By charging the machine at moments when it would normally be idling during operation, we can again reach continuous around-the-clock operation with either battery technology without any impact on terminal performance," notes Nurmela.
Managing peak loads
Kalmar electric straddle carriers are available with industry standard CCS1/CCS2 charging interfaces as well as with Kalmar's inverted pantograph charging system. Both solutions can be used for either battery technology. The automated FastCharge pantograph system is developing rapidly and can currently handle charging at currents of up to 1,000 A. Up to two machines can be charged simultaneously at a single FastCharge mast.
"In operations that utilise High Energy batteries that are charged during lunch breaks, the overall terminal infrastructure and electrical supply needs to support the simultaneous charging of the whole fleet," says Aki Heikkinen, Sales Development Lead, AMEA, Kalmar. "On the other hand, if using High Power batteries with faster opportunity charging, the terminal will have lower peak power consumption, but the charging infrastructure needs to be distributed in operational hotspots around the site."
In operations that utilise High Energy batteries that are charged during lunch breaks, the overall terminal infrastructure and electrical supply needs to support the simultaneous charging of the whole fleet.
The differences between required peak power can have a significant impact on the choice of charging solution. An electric straddle carrier uses an average power of around 50 kW, so a typical fleet of 50 machines would consume 2.5 MW of power during normal operation. If charged simultaneously with a 350 kW CCS2 charging interface, the same fleet with High Energy batteries would require a peak power of 17.5 MW during lunch breaks. With 10 FastCharge stations charging the same fleet of 50 machines with High Power batteries during operations, the system would require only approximately 6 MW of peak power.
In a FastCharge-based electric straddle carrier system, Kalmar's scope of work would typically include delivery of the container-based charging stations, as well as the pantograph equipment and their masts. The FastCharge station is powered by a medium-voltage power supply and is delivered with the necessary transformer and switchgear included. The terminal infrastructure is generally handled by the customer, so the terminal would need to consider factors such as the location of the charging interface in the yard, the foundation works for the station and mast, as well as the electrical, cabling and connectivity work needed at the site.
Charging at the right time
Kalmar FleetOptimiser for automated straddle carriers is a KalmarOne automation system solution for job scheduling and dispatching. The solution can also handle the assignment of charging tasks for automated equipment based on the specified parameters.
"FleetOptimiser basically schedules and dispatches the charging events in exactly the same way as the container moves," says Aki Heikkinen. "The solution also monitors battery levels and energy consumption across the entire fleet, ensuring that all machines are charged when needed. In addition to maintaining appropriate charge levels for all machines, Kalmar’s FleetOptimiser also optimises the usage of charging stations in order to avoid congestion."
FleetOptimiser basically schedules and dispatches the charging events in exactly the same way as the container moves.
For manually operated straddle carriers, the Kalmar ChargeOptimiser solution offers similar functionality. Both solutions can also consider changes in electricity costs to find the best time of day for charging.
Evaluating the overall impact
The main difference in total cost of ownership between hybrid and electric straddle carriers is the significantly different balance between capital and operating expenses. Electric straddle carriers require an approximately 30% higher initial investment due to the cost of the batteries and chargers for the equipment. However, they also offer an approximately 20% lower annual operating cost thanks to savings in energy and maintenance expenses.
"Over the long term, electric straddle carriers offer a very competitive total cost of ownership," notes Mikko Nurmela. "Once opportunity charging is built into the natural flow of operations, it will mitigate any performance impact of electrification. So, it is quite realistic to expect that a terminal wouldn't necessarily need any additional machines when transitioning to electrified operation."
Over the long term, electric straddle carriers offer a very competitive total cost of ownership.
Proven in action
Kalmar electric straddle carriers are already in service at multiple terminals around the world. At DP World London Gateway, Kalmar recently delivered eight fully electric straddle carriers with High Energy batteries, served by two FastCharge stations. The machines are fitted with both CCS2 and FastCharge charging interfaces and are able to operate for four hours with one-hour charging breaks.
At ECT Rotterdam, two new Kalmar electric straddle carriers will support the terminal's goal of achieving emission-free operations at its key terminals by 2035. The terminal is about to pilot one Kalmar electric straddle carrier with a High Energy battery and one with a High Power battery. The machines are charged from a single Kalmar FastCharge station.
At APM Terminals Pier 400 in Los Angeles, two electric Kalmar AutoStrad™ will be supplementing an existing fleet of 132 AutoStrad™. Two additional Hybrid AutoStrad™ are being retrofitted with High Power batteries. The machines are charged with two FastCharge stations.
"One of the benefits of the Kalmar straddle carrier is that it's designed as a modular machine," notes Aki Heikkinen. "So basically, we are just exchanging the hybrid power unit with a fully electric high power battery pack and its associated systems. The initiative at Pier 400 has been a particularly interesting pilot project, and we are really excited to see the long-term results from our customer on this one."
One of the benefits of the Kalmar straddle carrier is that it's designed as a modular machine.
A change in mindset
Electrifying a straddle carrier operation is a wide-ranging task that calls for a shift in perspective for terminal operators.
"It's not only about the equipment itself, but also related to the way you are operating today, as well as how you can utilize your operation in the best possible way in the future with electric equipment," says Karri Keskinen, Head of Global Sales, Horizontal Transportation, Kalmar. "At the moment, Kalmar can offer two alternatives for battery technology, based on either opportunity charging for hot seat operation or shift change type scheduling. The best choice will depend on the individual operation of the terminal or can be a combination of the two.
"Electrification is no longer just about the machines," adds Mikko Nurmela. "It's about the wider ecosystem within which we need to consider all the options and opportunities, whether these relate to new technologies or energy sources. The market is developing very fast, so we'll certainly see more innovations in the field within the next two to three years."
Related articles
Further reading
Subscribe and receive updates in your email
Subscribe